Just over 500 metres away from Ezhimala railway station at Kunhimangalam, Kannur, hidden from the rush of the city, nestled in a residential area with untarred roads flanked by shrubs gradually infiltrating the paths, around 11 artisans are at work under the shade of an asbestos shed, surrounded by heavy machinery and figures of deities cast in metal. The artists or moosaris are engaged in different steps of idol making using a technique which boasts centuries of history, that can even be traced back to the Indus Valley Civilisation, called the lost wax technique.
Among them, sitting cross-legged at the centre, is P Valsan or Valsan Kunhimangalam as he prefers to be called, who has been around metal, mud and the craft that binds them together since he was a child. Once a college lecturer teaching computer science, Valsan, returned to his ancestral trade full time over a decade and half ago, despite doubts from his family members, to keep alive the legacy of the craft with the help of his peers.
After finishing pre-degree, Valsan did a software engineering, and electronics and hardware diploma course. He then joined a private college as a computer science lecturer, where he taught for 10 ten years till he was 34. Even during those days after work, Valsan says, he would spend hours in the shed sculpting idols, lamps and even spittoons among other things.
Unfortunately, as the years progressed, Valsan witnessed his beloved trade lose sheen as artisans gradually moved on to other jobs. Once home to more than 100 artisans, currently, there are around only 30 artisans residing in Kunhimangalam practising the trade of idol making using lost-wax technique.
Ultimately, this saw him returning to sculpting and working full-time for the development of this craft. “When people in the locality stopped doing this work, 13 of us formed a bronze heritage trust, requesting the government to give encouragement to sustain this trade pointing out that the art is indigenous to this region,” says Valsan.
Wax model of Durga Parameshwari idol made by Valsan
| Photo Credit:
SPECIAL ARRANGEMENT
The trust kept petitioning the government and in 2014, the then Minister for Rural Development, Planning, Culture and NORKA, KC Joseph promised to set up a heritage village in Kunhimangalam and the Kerala Folklore Academy was assigned to study more about the village and its indigenous craft under a submission made by Kalliasseri MLA TV Rajesh in the legislative assembly.
In 2018, artisans led by Valsan formed a cluster, Kunhimangalam Bell Metal Heritage Private Ltd. (KBMHPL),with a grant of ₹1.40 crore. Seventy per cent of this allocation was approved by the Union government and the rest by the State government. The grant has been integral in establishing a common facility centre and populating it with machinery to ensure safety for the artisans. Ultimately in the same year, Kunhimangalam was awarded the status of a heritage village by the Kerala state government and the bell metal (a type of bronze) sculpting done by the Moosari community a heritage art.
Celebrated by all
Earlier this year, P Valsan sculpted a lamp cast in bronze, weighing 12 kilograms with a height and width of 15 inches, encasing an idol of Lord Ram and it was given as an offering to the Ram Mandir at Ayodhya, bringing nation-wide attention to the village.
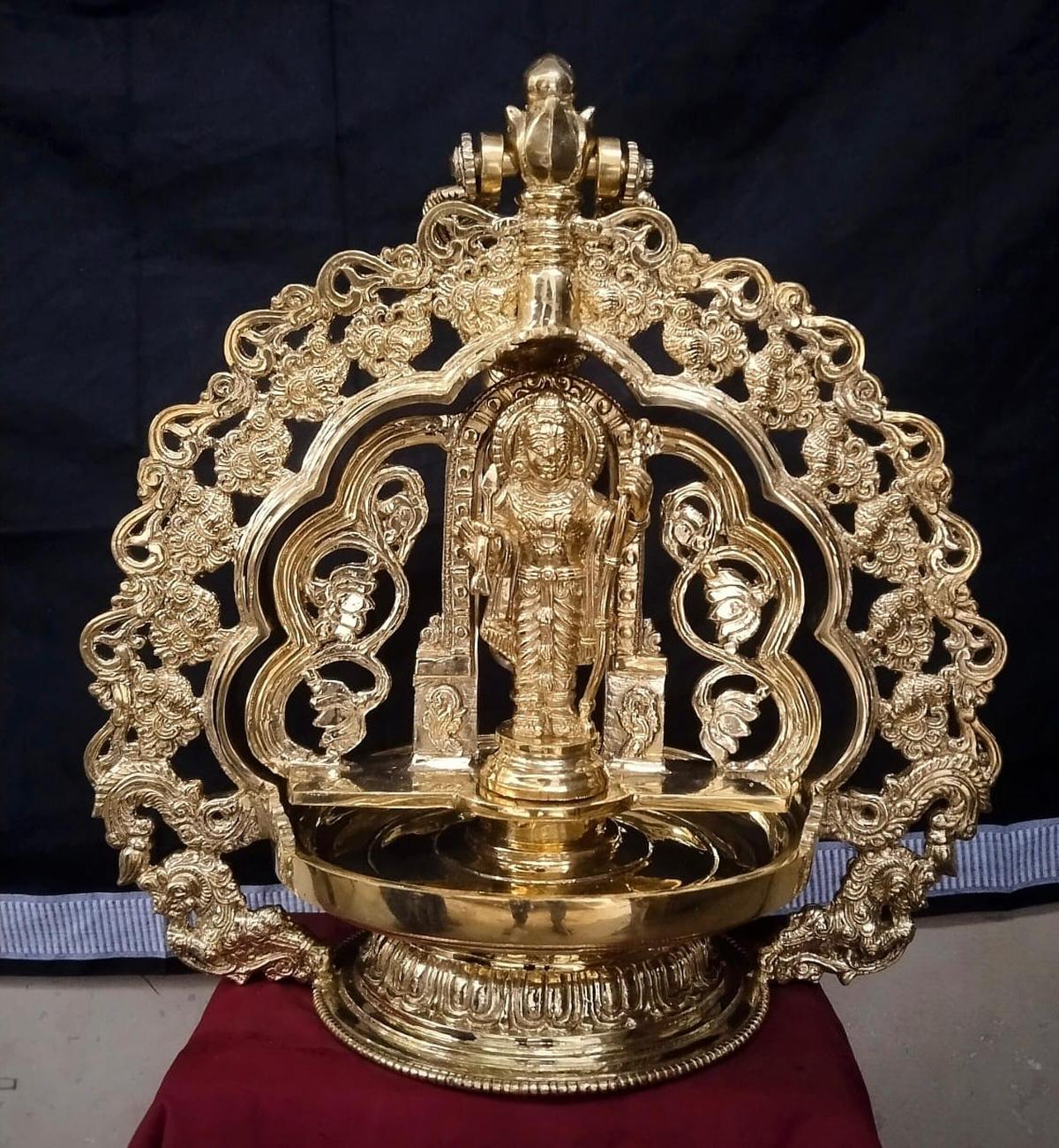
Ram Lalla Diya made by Valsan which was offered to the Ayodhya Ram Mandir
| Photo Credit:
SPECIAL ARRANGEMENT
Different types of idols, depending on the deity, its position in the temple, ie whether it will be installed as moolavigraham or central idol or balibimbam or ulsava balibimbam, meaning the one to be taken around in processions, and occasions are made in Kunhimangalam by Valsan and his cluster. Ornaments which are adorned by the performers during Theyyam, a Hindu ritualistic performance mostly seen in northern part of Kerala, are also made here along with cooking utensils such as an uruli, a traditional wide-mouthed, shallow cookware.
The skilful creations of the artisans here are celebrated across religions and regions. Valsan says, “All religious communities use the products we make. Churches need huge bells. Sometimes, they need us to make figurines of the Christ on a cross. People from Muslim community reach out to us make the minarets and crescents found on mosques.”
In recent years, says Valsan, the artisans have observed a rise in flow of tourists from the US, the UK, France and other countries.They have also had international customers for their work. “People from around 18 countries including those doing research or pursuing craft and fine arts come here to study the process. Last year, around 4,000 people visited us to know more about the technique,” says Valsan.
Lost wax techinque
The process of idol-making begins on a suitable day at a specific muhurtham or auspicious time. The idols can be made of any metal such as gold or silver and even panchaloha, an alloy of five metals, gold, silver, copper, zinc and iron.
The first step is making a wax model of the idol, the base around which the mould is built. This wax is a combination can-wax, charcoal, and resin, and it is shaped according to desired dimension of the article they are trying to make. For gods and goddesses, the ratios are mentioned in ancient texts known as dhyana slokas, says Valsan.
Once this wax model is prepared, different layers of mud are deposited on it. “The first layer is called mezhupurath mannu which also contains particles of cow dung. It helps the mould to hold its shape,” says Valsan. “Another layer of mud known as parumannu is put on the structure, which is further strengthened by iron rods and bars,” he explains. Then, a third layer of mud called madodu mannu, containing clay, jute, shards of roof tile and so on, is added on top of the previous layer. This layer sustains the mould’s heat and prevents it from breaking as well.
Once it dries, the structure containing layers of mud and the wax model inside is heated till the wax melts and leaks through a small opening facing downward called athrakaal. Once the wax is entirely melted, the mould is further heated and strengthened while the metal used for idol is melting.
The hot mould is partially buried into the ground with the athrakal facing upward and molten metal is poured through it, after ensuring that there is no mud particle stuck inside. Once the metal is poured, it is cooled down. “While it takes one or two hours for small idols to cool down, big idols take a day. After it cools down, the structure containing the mud and metal is dug out from the ground. The solidified mud is broken by knocking it with a hammer. After the mould is shattered, we get an unfinished form of the idol which is later polished and chiselled,” explains Valsan.
“It takes around a month to make an idol that is 12 inches tall with all the processes,” he adds.
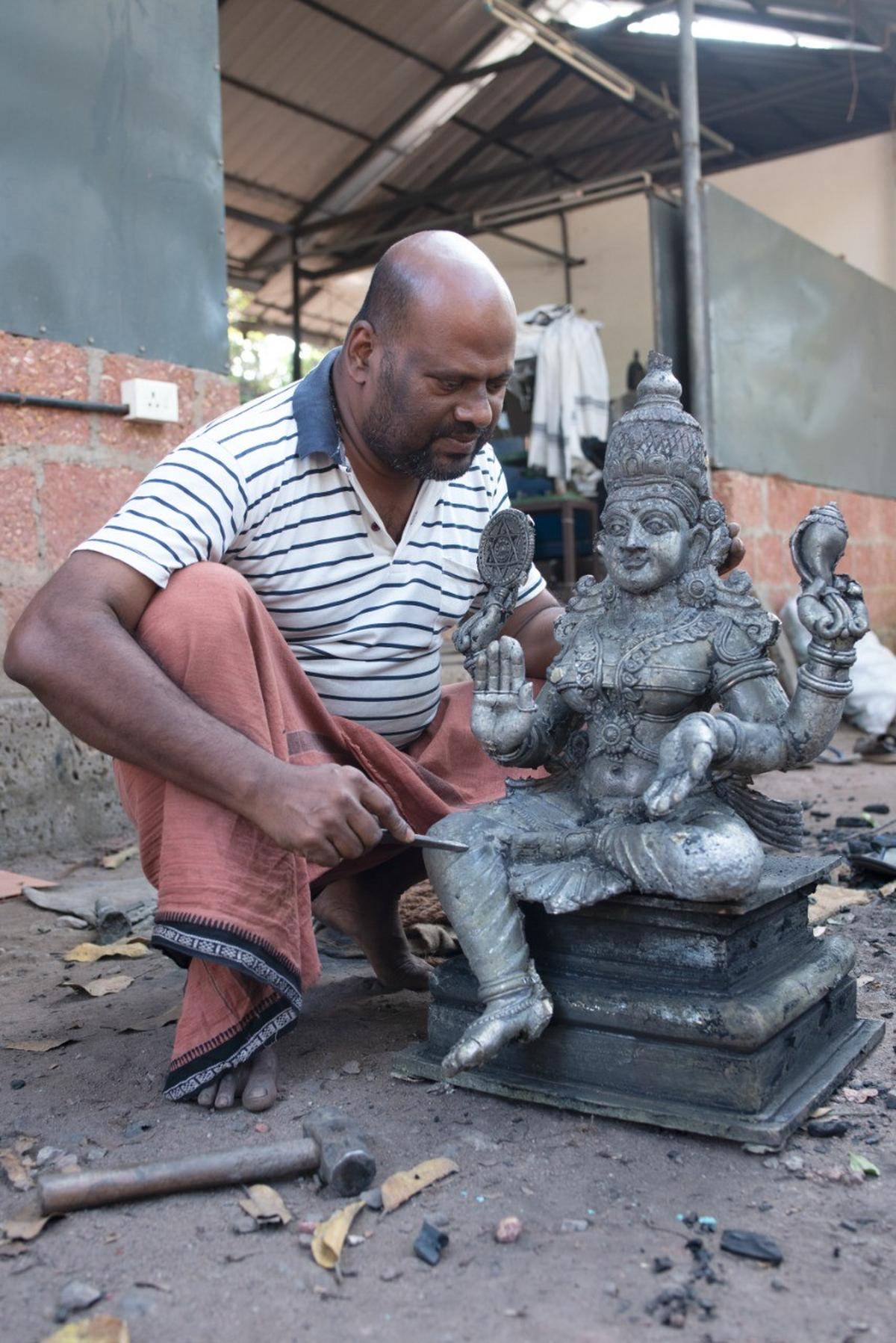
Valsan Kunhimangalam with an incomplete idol of Durga Devi
| Photo Credit:
SPECIAL ARRANGEMENT
Challenges
However, despite constant efforts, Kunhimangalam artisans are struggling to find more people to take up the craft. Valsan says, “It does not have a consistent flow of income or work. It is labour intensive and you will only be rewarded after you are done with the work and it might not be enough either.”
Valsan, currently in the quest for obtaining Geographical Indication status for Kunhimangalam, won awards from the Kerala Folklore Academy and Kshethrakala Academy for his bronze idol making skills in 2022. The artisan points out how such recognition can make this craft popular. “Maybe, if people realise that we can earn money from this, that this trade is recognised and it is important to preserve it, then more hands will turn up to learn this profession.”
Growing up, Valsan says he was not supported by his father and first guru Chandu to take up this trade. He says, “Even my brother tells me that our father incurred losses because of this trade , to be cautious.”
However, Valsan says he is supportive of his children as Vaiga, 14, and Vasudev, 8, who at times join him in the workshop. “They stand beside me and observe when I am working. They do know what kind of tools and metals we use. There are certain terminologies associated with this trade, which is understood only by people doing it. My children are also familiar with these terms.”
Published – November 27, 2024 02:41 pm IST